Some who follow my blog know of several articles about resawing boat lumber. I’ve found various hand tool resawing techniques around the Internet, but they are usually for relatively short boards. My interest is in boat lumber, often as long as 16 feet and sometimes longer.
Many hours sitting on the sawbench and a good stack of resawn lumber has brought me to the point where I can now pull my experience together as a tutorial. That’s not to say I think myself expert, but only that I’ve learned enough to feel basically competent. There’s more to learn before claiming real proficiency. This information will help those who want to resaw lengthy pieces of softwood lumber using hand tools. It may or my not help others. For example, I don’t know how well these methods will work for tight grained hardwoods.
So, why resaw by hand? First, the Atlantic white cedar I use for boat lumber is more than twice as thick as I need for planking and deck material. Slicing it doubles the value of each board. I’m a skinflint who likes to avoid buying more than I need. Second, my band saw is an entry level machine that would need significant investment to get the capacity and horsepower needed for lumber up to 12 inches wide. Third, I’m a skinflint Neanderthal galoot and would rather do it myself than pay the lumber mill. Fourth, this is a hobby, not a business where time might be more important. Fifth,my hand tools are powered by Snickers Bars, and the more I use them, the more Snickers Bars I can work off.
I’ll tell you what I’ve learned about making and tuning a saw, about holding the work pieces, about prepping a work piece, and techniques for getting good results.
Before going on, I have to recognize and thank several people. THANKS to Bob Smalser for his saw straightening and rehab tutorials on the Sawmill Creek forums and elsewhere, to Junior Strasil, also on Sawmill Creek, for his work holding and saw filing suggestions, to Peter Taran for his saw sharpening primer on the Vintage Saws site, to Josh Clark for his article on making a frame saw, and to many others who have added to discussions on the forums and in my blog comments. My success results largely from learning from these folks who graciously share their knowledge.
The Saw
My frame saw is made of oak almost exactly as Josh Clark described in his article. His design has given me a frame that is very strong and easy to handle.
Since the post about building the saw, I am on the third blade. The first was a very nice blade about 1 3/4 inches wide and quite thin. I now know that it is a “peg tooth” design (Thanks to “Saint Roy for that” definition) and is not really optimal for rip cutting. It worked OK, but slowly. Next, I tried a 3/4 inch wide 3 TPI band saw blade. It cut much faster, but also went wildly astray just as fast. The current blade is 2 inches wide, cut from a 1915 era Disston D-8 rip saw.
One of Junior Strasil’s suggestions was to file the saw teeth at 90 degrees instead of the usual 82 degrees (0 degrees of rake instead if 8 degrees of rake). This produces a more aggressive angle of attack and has worked very well. However, I had never ever sharpened a saw, and that meant learning how. I found Peter Taran’s “Saw Filing – A Beginner’s Primer,” an excellent guide. It suited my learning style. That old D-8, a few inexpensive tools, and some patience turned a reasonably decent saw into something I call “wicked sharp.” For example, when using this blade for normal ripping of 4 quarters cedar, a gentle nudge and the weight of the saw cuts about an inch per stroke.
While refiling this blade, I removed most of the set. The first couple of feet of resawing proved to “sticky,” so I added some set. Then (of course), it wanted to drift to one side, so I stoned that side. That first board has a good bit of “wandering” as I learned to tune the saw. That’s OK. I need some really thin boards for decking.
The end lesson in all this rambling about the saw is that saw sharpening is not that difficult. I see it as a gateway skill that any hand tool woodworker should be able to easily learn. The next time your saw needs sharpening, don’t send it out. Do some reading at Vintage Saws, order some files and learn a new skill.
One last suggestion. When you make your own saw, be sure to give extra attention to making edges comfortable to hold. For this kind of work, your hands will spend lots of time at the upper reaches of the uprights, and at the outer ends of the top piece.
Workpiece Prep
The cedar I use is purchased as live edge flitches. Each board is rough sawn, about 4 quarters thick, and still has bark on the edges. For each flitch, I find the widest width of heartwood I can get from it and strike chalk lines for the waste that’s to be removed. If the board is narrow enough to fit within the frame saw, I use it to rip to the lines, about 3 or 4 minutes work for each 16 foot edge. If the board is too wide for the frame saw, I put the board vertically on the front apron of my long workbench and rip with a bow saw. Depending on how careless I was sawing, a few minutes with a jack plane might be needed.
The most important part of the prep is marking center lines on the edges. I use a center marking tool and scribe these lines about 3/16 inch deep and on all 4 edges. Yes, it is worth the effort to mark the ends (well, at least one end) as well as the long edges. These deep and easily visible scribe lines are critical to getting good results.
Lastly, I mark distances in one foot intervals on the long edges. It helps quiet the idle child’s question, “Are we there yet?”
Work Holding
This had me a bit puzzled until I asked a question on one of the Sawmill Creek forums. Junior Strasil replied with a lengthy answer that led to the solution I’m using now. I already had two very nice saw benches that I built from plans by Chris Schwarz. They were a matched pair, both the same height, an important part of the answer.
I added two vertical guides to one of the benches. Those guides form a gate that holds a board vertical underneath the bench top. Wedges in the gate keep the board absolutely vertical. I originally used wedges under the boards to clamp the up against the bench top but have since changed to using a simple f-clamp instead. It’s faster and easier to set. Recently, a wider board wouldn’t fit, so I modified the cross braces of the larger saw bench to accommodate a notch for the wider board.
Wider boards also present another problem. There’s reduced room for the length of the throw. In some pictures, you’ll see the saw benched sitting atop 2 by 4s, offering a bit more throw.
The basic setup is using the bench with the gate at the end of the board being cut, and the other bench clamped to the other end of the board to keep the board relatively level. The two benches and me sitting on one of them is enough to keep the workpiece stable.
Sawing
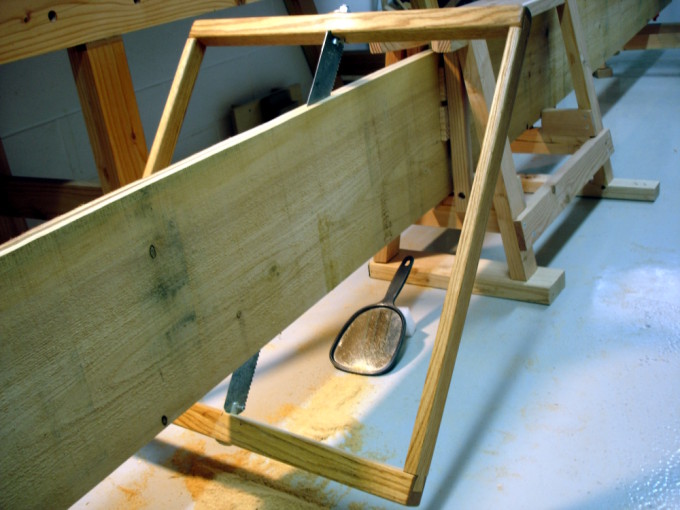
Start with the board extending 12-18 inches from the gate. Start the cut very carefully, using the scribe line on the top edge and the end to ensure as precise a start as possible. I have found several techniques useful in keeping the cut precise.
Watch the bottom of the cut with a hand mirror. Propping the mirror up at an angle helps keep it back from being directly under the cut and reduces the frequency you’ll need to clear off the sawdust.
Vary the angle of attack frequently. Sawing with the bottom edge moving away produces a long leading ramp inside the kerf on the top edge of the board. Raking the saw over in the opposite direction produces a long leading ramp inside the kerf from the bottom edge of the plank.
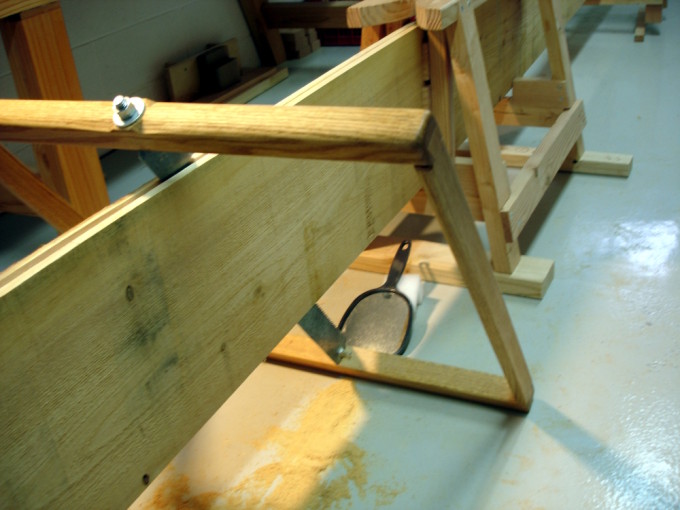
Use the mirror for this one. When you’re making a nice little curl directly from the center of the scribe line, the ramp is perfect. These ramps provide very effective guidance for the blade. Bring the blade vertical to saw away the apex of these two ramps.
Changing the sawing angles is also helpful for removing dust. There is not enough throw in the saw strokes to efficiently remove dust. That is, the tooth that starts a stroke does not continue all the way through the board to release its dust. The most dust clogging happens when sawing the upper ramp. One method that helps remove this dust is to rock the saw in an arc, kicking up the bottom with each stroke. The other sawing angles are much better for releasing dust. It really falls out easily when the saw is cutting the bottom ramp and at angles approaching that one.
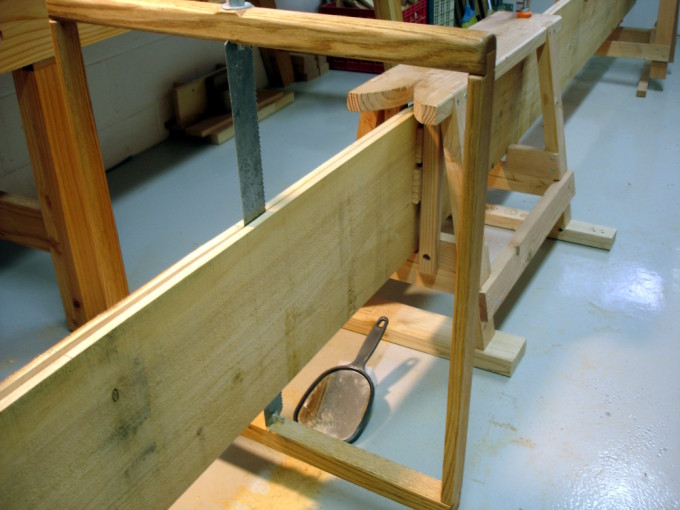
Changing these angles frequently does two things: the ramps provide guidance and the different angles of attack keep the sawing surface small and dust release effective. One might think that resawing a 10 inch wide board requires constantly sawing a 10 inch wide surface, just as a band saw does. I’ve tried it that way, and progress is much faster with the multiple angle approach.
Binding is a potential problem. The first few feet of every board produces the most pinch in the kerf. The boards want to pinch back together quite strongly until the cut moves in 3 to 4 feet. After the kerf becomes 3 or 4 feet long, tension eases and the kerf opens. Until then, thin wedges in the kerf can provide relief. It also helps to wax the saw occasionally. I use a simple candle for waxing.
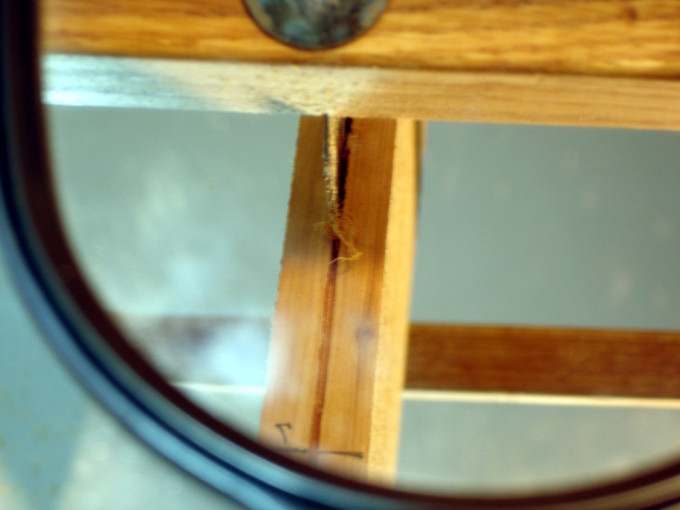
Sawing effort is moderate, and should be kept moderate. Anytime a saw is forced, it’s liable to bend away from the desired path. I have a few feet of lumber that proves that point well. When the saw is running smoothly in an open kerf and with good guidance ramps, it is easy to maintain a cadence of 60-70 strokes per minute without breathing heavily. Cutting rates depend on the width of the board. My cutting rate for an 8 inch board is almost 4 feet per hour. A 12 inch board drops to about half that. OK, OK, I hear you asking (again) if this guy’s crazy. Probably! But he’s working off those Snickers Bars.
As the Cut Progresses
We started the cut with a saw bench clamped to each end of the board. The gated bench starts, with the gate facing the end of the board, about 12-18 inches from the end of the board. As I sit on the end of the bench, I find 18 inches a comfortable reach. When the cut nears the bench, unclamp the gated bench and pull it back along the board another 12-18 inches. Recenter the board in the gate, Set the f-clamp at the tail of the bench and continue sawing. When the mid point of the board is reached, the cut ends of the boards are probably flapping around and maybe affecting the cut. That’s when it’s time to move the supporting bench from the tail end of the board to the other end.
Continue the process of periodically moving the gated bench until there’s no room to use a clamp. At this point, unclamp everything and rearrange the benches and saw so that the gated bench now has the gate facing the short end of the board, and the saw is trapped between the gate and the end of the board. It is very uncomfortable to attempt cutting by sitting on the bench and pushing the saw backwards. Get a chair of similar height and sit at the end of the board to complete the cut. Since there’s no body full of Snickers Bars sitting on either bench, some temporary weight or other constraint might be needed to keep the rig from moving. I sometimes toss a rope through the legs of the supporting bench and tie it to something immovable in the shop.
When the Cut Goes Astray
Oh, it will. This was a frequent occurrence on my first few boards. Saw tuning, and developing the multi-angle techniques have mostly eliminated the problems, but you need to know how to recover. Of course, constant use of the mirror helps spot the wandering before it gets serious. I used to keep the mirror on the bench beside me, and reach for it once in a while. After a few wanderings, I learned to keep the mirror on the floor and to watch it constantly. OK, back to recovery. Imagine that you’ve wandered off into day dreaming as you saw and the saw has wandered off too. You’ll see this at the bottom of the cut, not the top. (probability = 1.0) The best recovery I’ve found is to unclamp the workpiece and turn it over. Work at correcting the wandering from the top. Be forewarned that simply trying to use brute force to press the end of the saw back to the line will result in a nice long cupped section. Don’t ask how I know.
Next?
Some of the blog commenters have wondered whether a saw with fewer teeth per inch would cut faster. That’s very likely. A 3 tpi saw with deeper gullets might be faster. I don’t yet know. I’m at 5 tpi because that was the original filing of that old D-8 blade and it was an experiment, one that turned out quite well. I might get another old rip saw and try a 3 tpi, deep gullet version. For the time being, there’s a lot of thin spruce pieces needing ripping and I want to keep this 5 tpi blade for that work.
If there’s anyone reading this who also thinks resawing with hand tools is a good idea, leave a comment. I’d love to know there are other skinflint Neanderthal galoots around. What fuels your hand tools?